
“Cylinders that are 100 years old will be good for another 100 years if they are properly taken care of and maintained,” says Hydrostat Inc. Owner and CEO Stacy Schraut. “The beauty of the packaged gas industry is that we have assets that are 100 years old that can continue to generate revenue. How many other industries can say that?”
Compressed Gas Cylinders are over-engineered, due to the critical nature of their purpose, according to Airgenics, Inc. COO Jonathan Balbi. When properly maintained, these cylinders should last for hundreds of years. The key to this is proper maintenance coupled with mandatory cylinder testing as prescribed by the Department of Transportation (DOT), the Pipeline and Hazardous Materials Safety Administration (PHMSA) and the Compressed Gas Association (CGA.)
“Doing the absolute bare minimum will not extend the lifespan of a cylinder,” says Balbi. “It will only let you know that your aging inventory is going bad at an exponential rate. Companies that have kept good care of their cylinders still see them passing back into service. I have seen plenty of cylinders from the 1970s up to the 2000s fail expansion tests because of obvious neglect that could have been prevented for a lot less than the cost of a new cylinder.”
How Testing Works
The DOT and PHMSA regulate the transport of hazardous materials through Title 49 of the Code of Federal Regulations (49 CFR), subchapter C, “Hazardous Materials Regulations.” As mandated by CFR Title 49, “Each cylinder used for the transportation of hazardous materials must be an authorized packaging. To qualify as an authorized packaging, each cylinder must conform to this subpart, the applicable requirements specified in part 173 of this subchapter, and the applicable requirements of subpart C of part 178 of this subchapter.”
Every five or ten years, a standard DOT-rated cylinder must be requalified before it can be filled and transported by one of two accepted methods. The first method is a volumetric expansion test to determine the elasticity of the cylinders. The other option is an ultrasonic inspection that scans the cylinder and checks for defects in the metal and compares the average wall thickness against the manufacturer’s specifications and a calibration of a similar metal.
If the cylinder passes either of these tests and a visual inspection, it is deemed to be an authorized package and can be stamped and filled for another service cycle. Reject cylinders are condemned and destroyed as prescribed by the CFR 49.
Hydrotesting
“I’ve been an advocate in our industry for hydrotesting ever since our customers started pushing for more ultrasonic testing,” says Schraut. “In very rare circumstances, a cylinder has passed an ultrasonic test but would have failed a hydrotest. In the last seven years of ultrasonic testing this has happened on no more than three or four occasions out of more than 500,000 cylinders tested. That’s a very small number but in our opinion it’s still too high.”
A hydrostatic test involves vacating any residual gas from the cylinder, removing the valve, filling the cylinder with water, placing the cylinder into a sealed water environment, introducing pressure greater than that of the service pressure for a standard period of time (usually 30 seconds), releasing the pressure and measuring the expansion (permanent and elastic), removing the cylinder from the sealed environment, emptying the water, drying the cylinder, performing an internal visual inspection, stamping the cylinder and reinstalling an acceptable valve (usually the same valve that was previously in the cylinder unless it does not conform to thread count specifications or having a service change done.)
An ultrasonic test, by comparison, involves placing the cylinder in the ultrasonic machine and testing it under ideal circumstances (exterior in good condition, empty of liquified gases, valve closed.)
“Part of the requalification of a cylinder is to do an internal inspection on that cylinder, according to the 49 CFR,” Schraut says. “So, in my opinion if you’re not removing the valve for an ultrasonic test, you’re not really satisfying the guidelines of the 49 CFR.”
Says Balbi, “When you have removed the valve, a host of optional procedures are opened up and each one can extend the cylinder life if coupled with a good in-house procedure, so that the owner of the asset is ultimately determining the cylinders function. This does take some planning and forethought but can mean the difference between a reject asset and a good cylinder. If the asset base of a company is 40,000 cylinders of mixed manufacture dates, around 5,400 cylinder per year would need to be tested to maintain an in-service asset base, with an average of 45% of cylinders being over 60 years of age, without maintenance beyond standard testing expect to lose around 95 cylinders per year more than with above and beyond upkeep. In dollars that can equate to more than $20,000 dollars per year on new cylinders just to make up what is lost.”
What Should My Service Provider be Providing?
In the August 2019 GAWDA Monthly Safety Organizer, GAWDA DOT, Security, OSHA and EPA Consultant Michael Dodd wrote an article entitled, “Auditing Your Hydrotest Vendor.” In the article, he provided a checklist GAWDA member companies can use to ensure that the cylinders that you send out for requalification are being done properly and that the facility is in compliance.
At a minimum, the service provider should be able to provide an inventory of cylinders that are inhouse and what service they are in, including a breakdown by size and gas type, along with confirmation that the cylinders sent in can go back into the same service. (A good requalification company will know if they can put an asset back into a specific service. More often than is realized, a fair number of cylinders may no longer be able to go into a service that is needed.)
“If a cylinder fails a test and no longer can get a star or a plus rating or the cylinder’s age doesn’t allow it to get a star or plus rating, that doesn’t necessarily condemn it to be scrapped,” says Schraut. “Oftentimes a cylinder can be taken out of oxygen service or nitrogen service and put into CO2 service. That’s one of the ways you can extend the life of a cylinder is simply by changing the service that it is in, when it no longer meets the requirements for the service it was in.”
The service provider should also provide a copy of test reports with notations for work done to:
Assigned ownership notation
Manufacturer name
Manufacture date
DOT specification
Physical dimensions
Previous gas service
Notes
Required test pressure
Pressure reached
Required test time
Actual test time
Date and time tested
Operator name
Determined reject elastic expansion and source for REE
Actual permeant expansion
Actual elastic expansion
Marking eligibility (e.g., + *)
Pass/fail determination
If any data is missing, the cylinder may not be treated as though it is an authorized package. All of this together is what an authorized requalification company should provide with every order.
Asset Management
So why can a cylinder made in 1970 be condemned from service before a cylinder from 1904?
“It all boils down to asset management, storage and communication,” says Balbi. “Having a simple yet comprehensive plan in place to sort assets as they come up for service that encompass a packaged gas companies near future needs, anticipated growth sectors, and an effective prefill inspection that can isolate assets that requires a secondary service to extend total life, regardless of service date;
herein lies the difference between caring about cylinders and filling and billing.”
According to Schraut, asset management and distributors having positions dedicated to asset management is one of the biggest changes in our industry in the last 20 years.
“There are created positions now, where somebody is overseeing their assets to make sure that if a customer has an overabundance of oxygen cylinders in their inventory and a shortage of nitrogen cylinders, rather than spend $250-$300 per cylinder to buy 100 nitrogen cylinders, they can send those oxygen cylinders in and have them blasted and painted, washed and outfitted with a new valve and for a tenth of the cost of buying a brand new cylinder, they can get what’s functionally a new cylinder for a new service,” he says. “Rather than having those cylinders sitting out in the yard not being utilized, they’re sending them in to be converted to the gases that they’re in need of at the time.”
The unsure economic future of metal manufacturing as well as the turmoil in trade will make new cylinders more expensive with longer lead times for delivery. Now is the time to evaluate the age of your inventory and forecast any future needs. If planned properly, a company can maintain assets and keep them in service longer than originally anticipated, giving them a slight edge over the competition. Growing pains of purchasing new asset acquisition and shrinkage caused by asset misappropriation can be mitigated to figures that will allow for less capital investment in steel and more investments in infrastructure.
For more information on cylinder care best practices, be on the lookout for the follow up article in the 4th Quarter Issue of Welding & Gases Today.

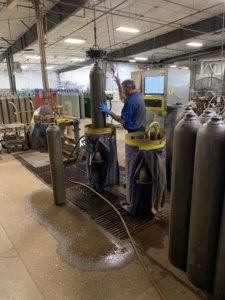